Managing Component Obsolescence
A Proactive Approach 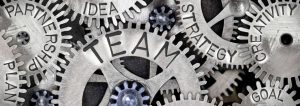
CMD engineers, technicians, parts & upgrades specialists and supply chain management collaborate to source replacements and resolve the gaps caused by component and parts obsolescence. Now, a new, proactive approach holds promise for faster solutions and enhanced support for customers.
Component obsolescence is considered a supply chain threat by most manufacturers. When a component or part is no longer available from the original manufacturer to the original specification,it is considered obsolete. Manufacturers today face increasing challenges of supply chain interruptions caused by many global issues, including the interruptions resulting from the pandemic. Add to that the ever-present impact of obsolescence, and the risk has grown considerably.
CMD has looked at the enhanced risks and has reviewed issues we have encountered with obsolete parts and components. A new cross-functional team has been established, and a program put in place to optimally manage obsolescence issues and provide more solutions and less downtime for customers
Technology is changing more rapidly
Technology evolves much faster today, resulting in a shorter product life cycle. In other words, gears and chains stayed current much longer than today’s electronic and digital components.Technological evolution generally makes older technologies less practical and eventually as supply diminishes, prices go up.
“We strive to be one step ahead of the advancing technology to anticipate the end-life of components,” says Curt Frievalt, CMD Project Manager. The new program will put the end-of-life (EOL) components and parts on the radar sooner, and the team will identify whether replacements are available on the market, or unique solutions are needed to forestall issues at customer facilities.
A Disciplined Approach
The good news is that there is a way to manage obsolescence and to minimize impact to CMD customers. Collaborating with suppliers, the CMD team – made up of procurement, engineering, operations and sales personnel – will meet regularly to identify any new EOL developments and to determine if suppliers have a ready replacement. If no ready replacement is available, an early identification of the EOL situation allows CMD’s technical team more time to proactively develop a new solution.
Determining the Impact
Since not all obsolete components have the same impact on CMD customers, the team will identify the impact and magnitude of the discontinued part, and if customized solutions are required, will prioritize those accordingly.
“The goal is to identify in advance and in a timely manner, a better, most cost-effective solution, and to minimize or eliminate customer inconvenience and downtime,” says Dane Dorn, CMD Manager of Supply Chain and Continuous Improvement. “The program includes a notification process to get up to 2-years advance notification from suppliers of impending EOL situations.” This advance notification system will provide CMD with a better transition for replacement and timely, efficient solutions for customer. “We want to confirm that the supplier’s replacement is the best option for our customers,” notes Dorn. “It’s not always a one-size-fits-all solution we are looking for.”
Longer Advance Notification
As always, clear and consistent communication is at the heart of any effective program and sending out alerts earlier to customers is a major goal of the new program.
“We are looking at potential issues earlier,” says Troy Hoehne, CMD Spare Parts Sales Manager. “The program will include email notifications when obsolescence issues could pose a potential issue for ready-replacements for customers.”
Customized Solutions
Customers have CMD machines in operation for 20 or 30 years, sometimes longer. The array of obsolescence issues and potential solutions is varied. CMD draws on an experienced bench of engineers and technicians to develop these unique solutions.
“We have a robust team with seasoned engineers with legacy knowledge collaborating alongside bright young programmers with new ideas and solutions,” says Frievalt. Obsolescence issues are likely to accelerate with technology evolution. CMD is committed to shoring up internal processes to deliver timely and cost-effective solutions to keep our customers up and operating at peak efficiency.
Helpful Resources
-
Take advantage of CMD support services, like optimization and equipment audits, to better predict and plan for parts and maintenance requirements
-
Consult your CMD spare parts professional to discuss your safety stock and any critical part inventory requirements
-
Ask about CMD Insights – a customizable data management tool that delivers real-Time actionable data
For more information, contact Austin Laber at +1 (920) 380-8326.
Leave a Reply